Dear Guest,
Please register or login. Content don't create itself!
Thank you
-
-
Headbadge development.
The original idea for this head badge was for it to be gold, silver and bronze so I started out using a copper base and played with silver and gold inlays using PMC. This turned out to be every bit as difficult as it sounds and the $100 per gram price on the 22k gold is a bit of a deterrent. The death knell was that once polished the contrast between the elements was not sufficient to show the detail of Chooey’s lovely avatar, so I turned to using just the silver.
I decided to use four nines fine silver (99.99%) rather than the more common sterling silver as it has better resistance to tarnish and the lower strength is actually a benefit as it is easier to form to shape. After playing with a few alternatives I decided on a scheme of etching or chemically milling the design into brass sheet and using this to form the silver.
First job is to transfer the design, using transparent film and an ordinary printer. Since the printer coverage is less than 100%, better results are obtained by overlapping two films.
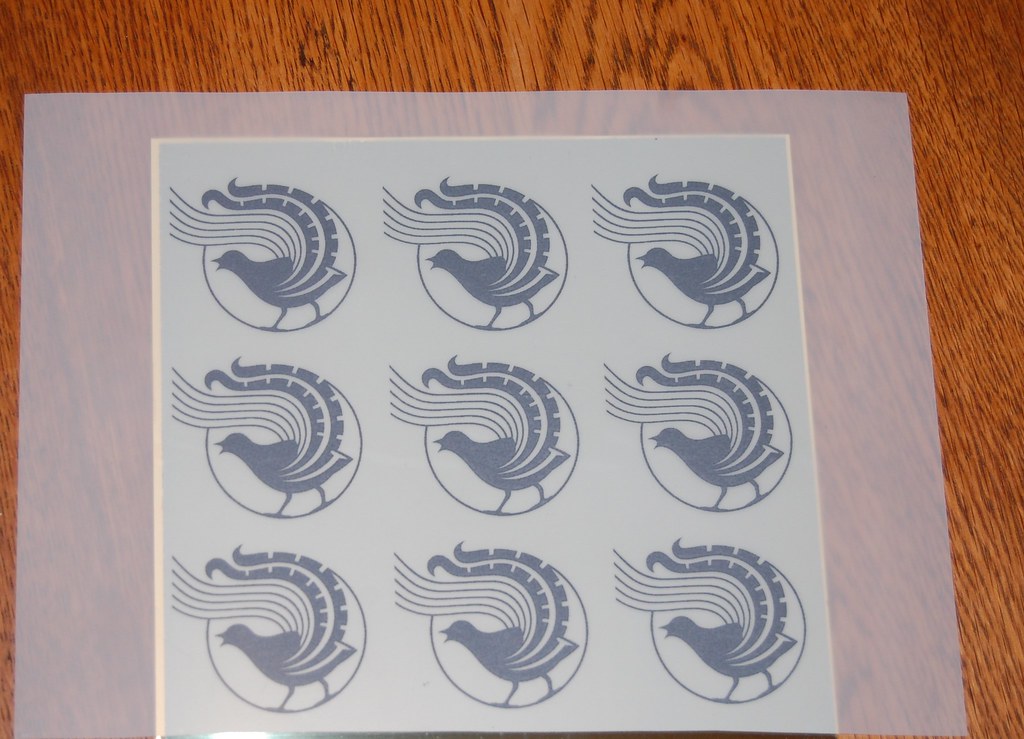
[url=https://flic.kr/p/GnMebs]Overlay
The brass sheet is then laminated with photolithographic film, I used DuPont Ristron 500 series. The extra bit of film is to help with judging exposure.
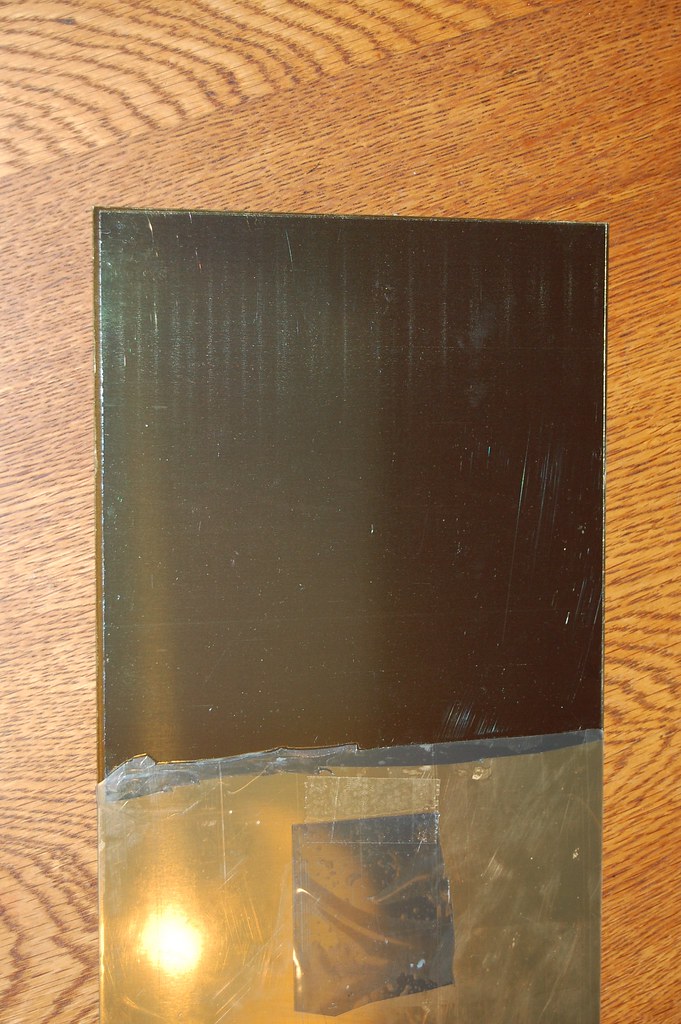
Brass + film
The printed sheet is laid ink side down on the film and exposed to UV until the exposed areas crosslink, then a mildly alkaline developer fixes the exposed film whilst loosening the non-exposed areas, creating the mask:
Etched and Developed by Mark Kelly, on Flickr
This is etched in iron(III) chloride to 50% of the sheet depth. Note that the previous pics were taken on the first run, the rest are on the second run where I added the border to make dividing the parts easier:
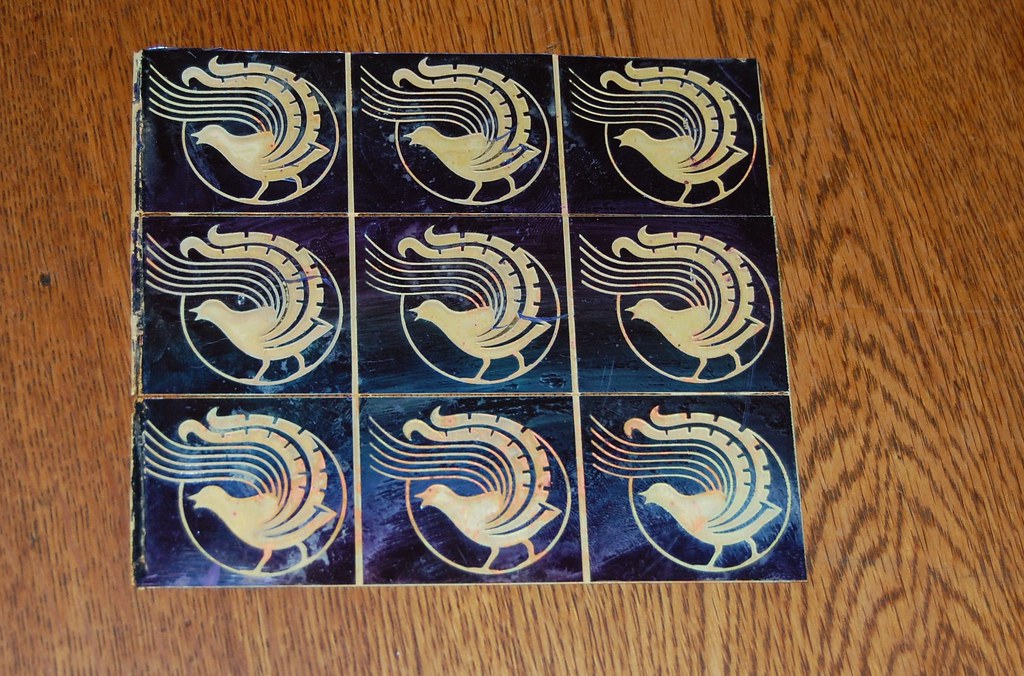
Etched 2
The mask is removed with ethanol:
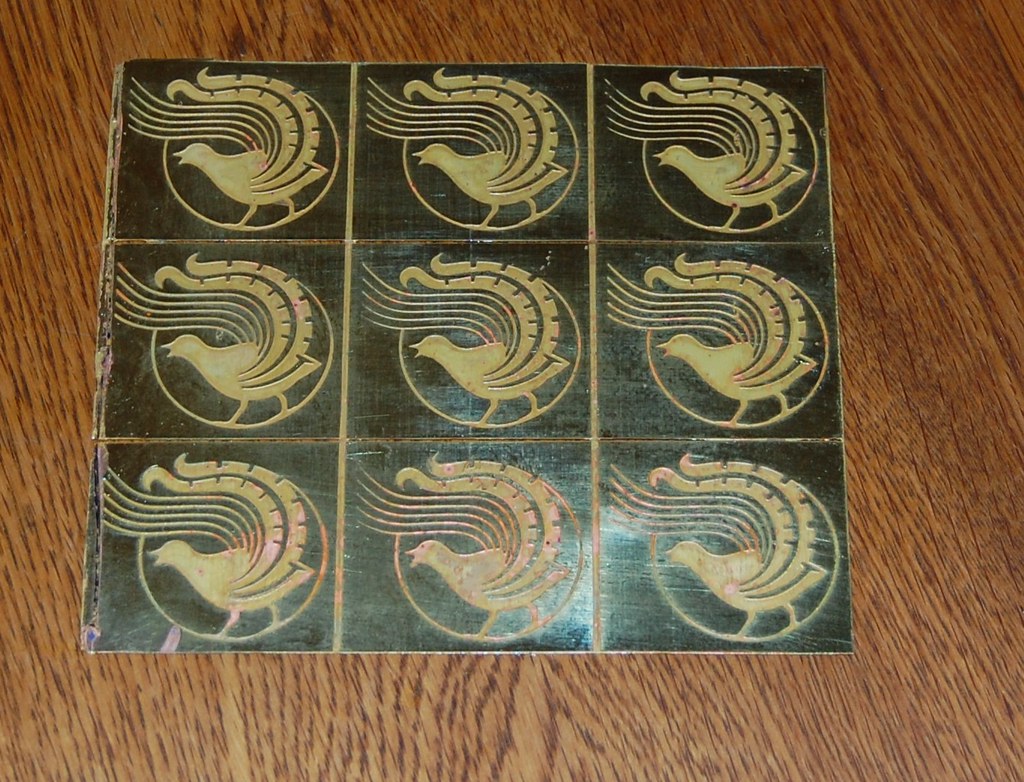
Stripped
The sheet is then re-etched for a few minutes to matt down the polished surface. BTW the reason you can see through the borders here is that the back of the sheet is also masked off except at the borders, this helps with judging etch depth (when they meet it's 50% each side) and makes the parts easy to separate.
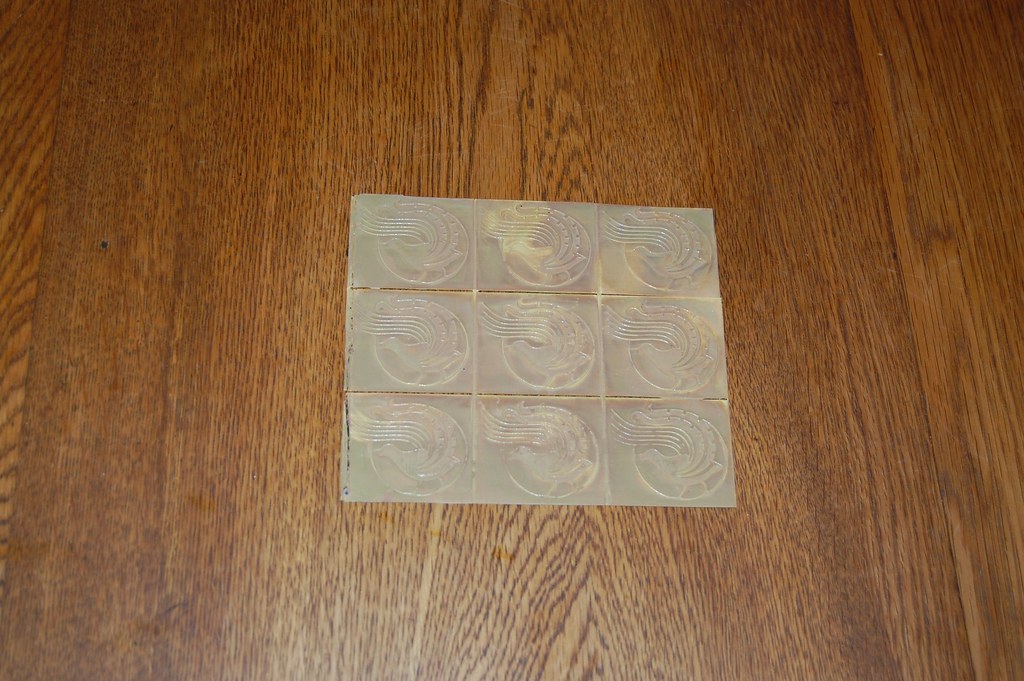
Re-etched
The now complete negative is matched up with an equivalent sized piece of silver sheet:
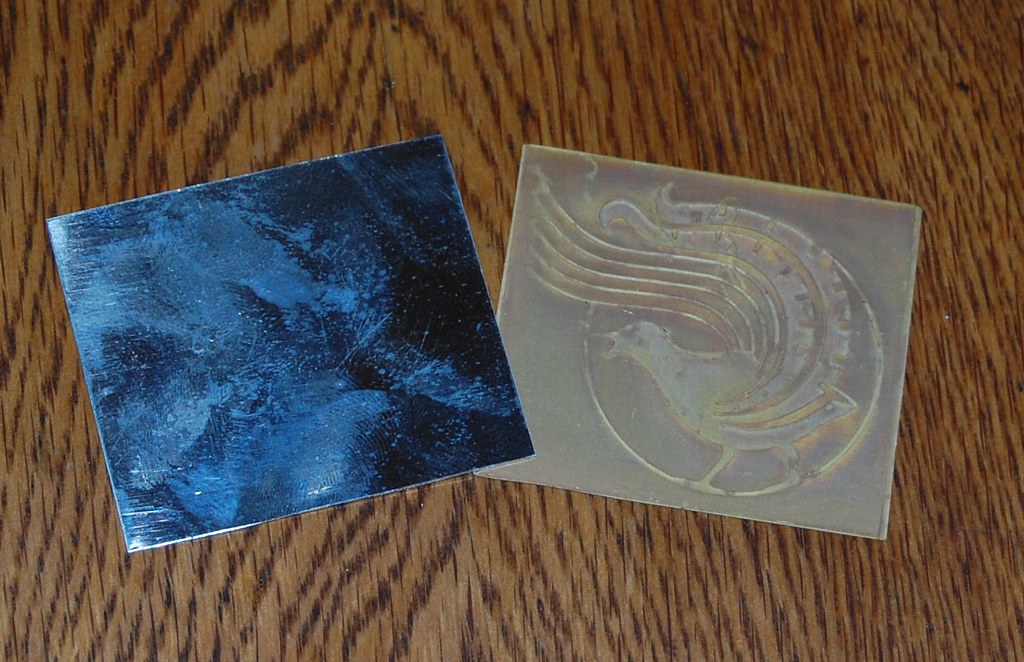
Silver and Form
The two are then hand beaten with an ordinary hammer and anvil to force the silver to conform to the milled cavity. Note that the beating causes a bit of deformation at the edges, I actually like this effect:
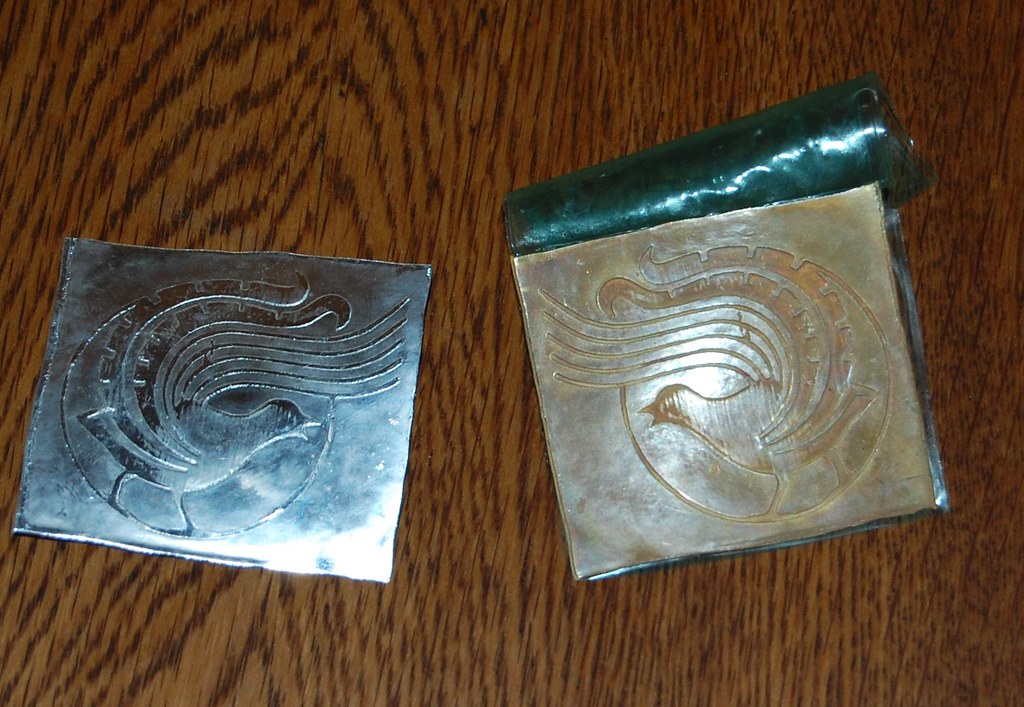
Silver Formed
To improve contrast I decided to oxidise the backround using potassium sulphide (KS), known in the jewellery trade as “liver of sulphur”. To prepare the silver for this the sheet is first polished, then the haut relief is burnished with agate, then it is polished again. Finally the haut relief is masked with a resistive ink pen:
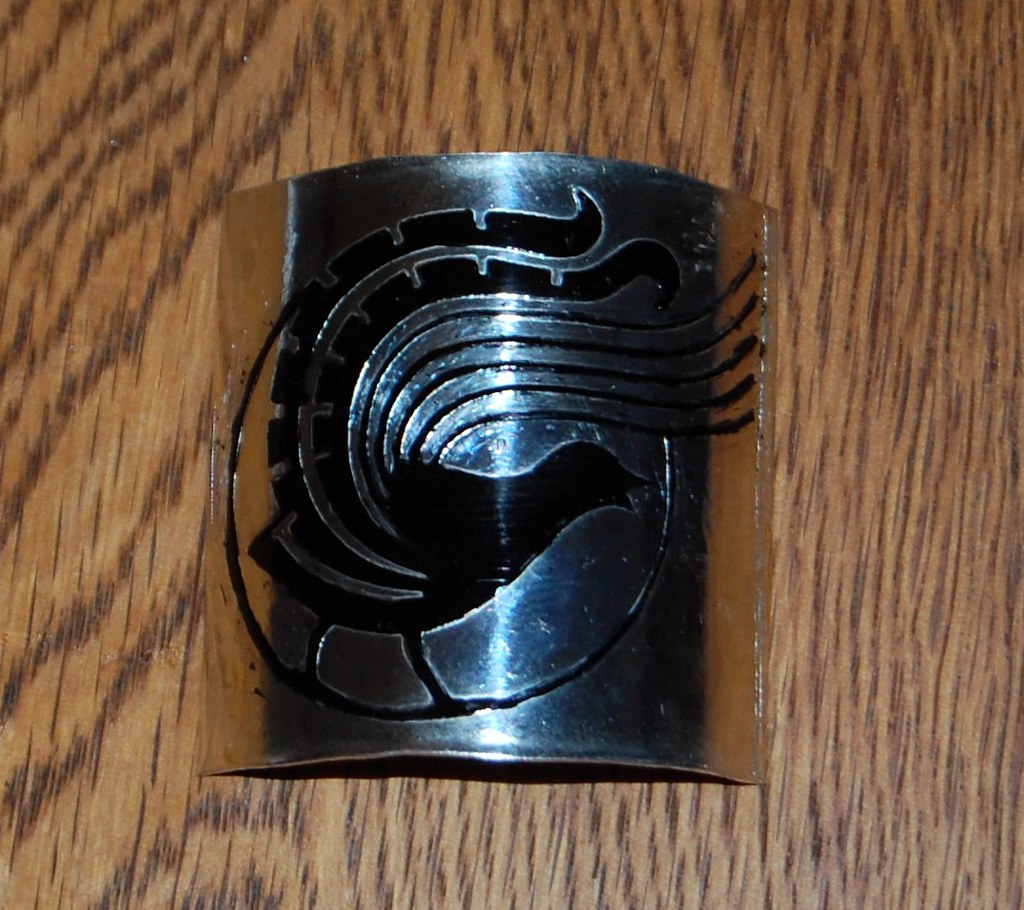
Masked
The masked badge is then exposed to the KS solution until the required depth of colour is reached, then neutralised and polished again.
Enough with the polishing already.
The final thing does justice to Chooey’s design, which is more than can be said for my terrible photography:
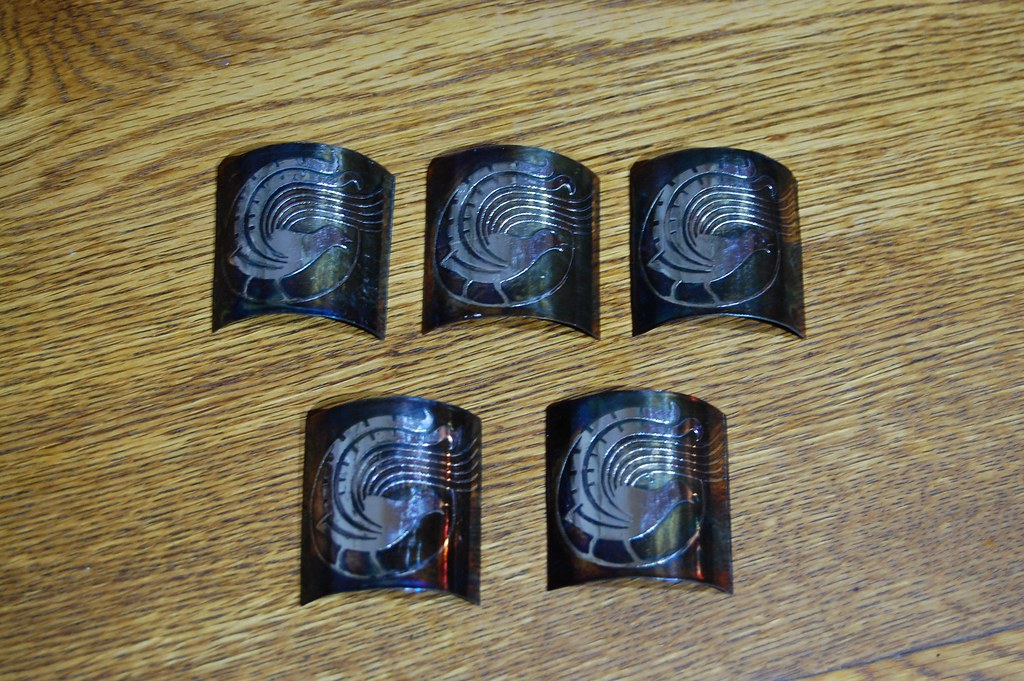
A Flock of Lyrebirds
Since I already had the outrageously epxensive 22k gold on hand, I tried adding burnished gold to highlight the display feathers:
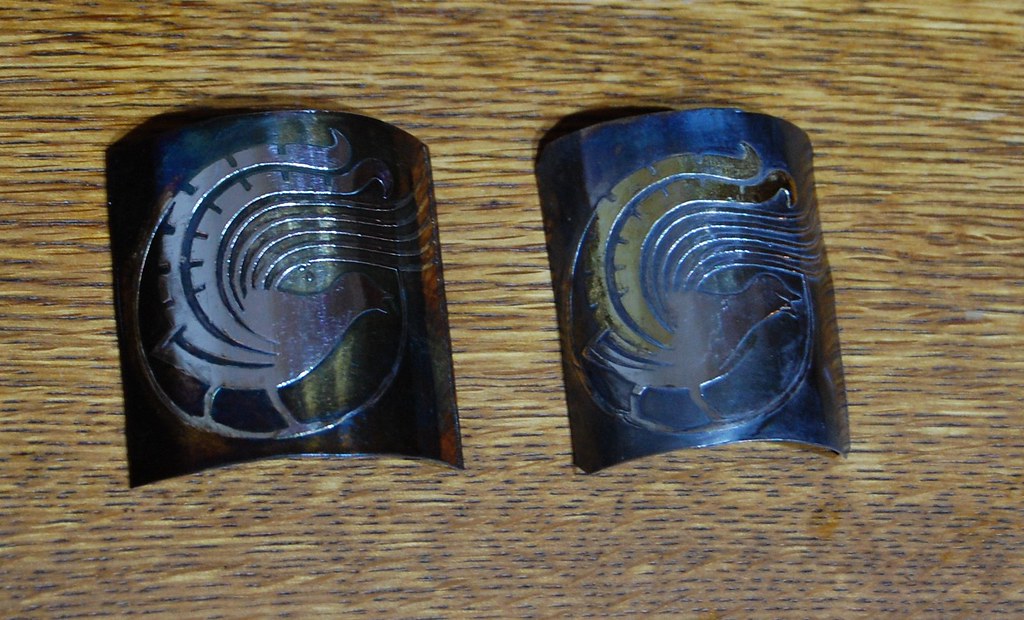
Silver and Gold
I'm sticking with the straight silver.
Mark Kelly
-
Re: Headbadge development.
Something I left out: obviously between the hammering and the sulphide treatment the flat silver is curved to fit the head tube. Since four nines silver is quite soft even when work hardened by hammering, this is done by pressing the piece between a 31.75 mm PMW tube block and a chunk of 30mm aluminium rod.
Mark Kelly
-
Re: Headbadge development.
Mark Kelly
-
Re: Headbadge development.
Holy crap. Now that's a process. Wow.
At the end, what are your thoughts? Are ya digging it? Improvements?
-
Re: Headbadge development.
Was that in reference to the bikes or the headbadges?
Assuming the latter, I'll use what I've got and see how they hold up. I think I will have to protect them from exposure to the elements so I'll use the lacquer I used to use on the brass faceplates of the audio equipment I built. It's called Like Armour and is made by an Australian mining products company called AROA: pdf here.
Mark Kelly
-
Re: Headbadge development.
K took a few pics of her bike yesterday, here's one.
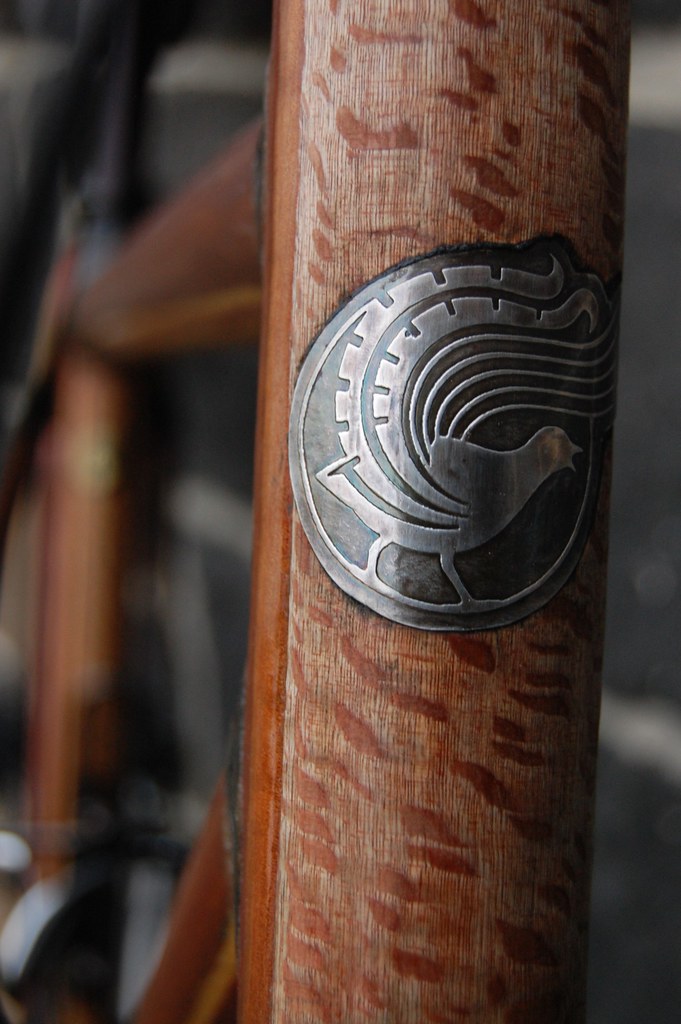
Mounted
Mark Kelly
-
-
Just a pic
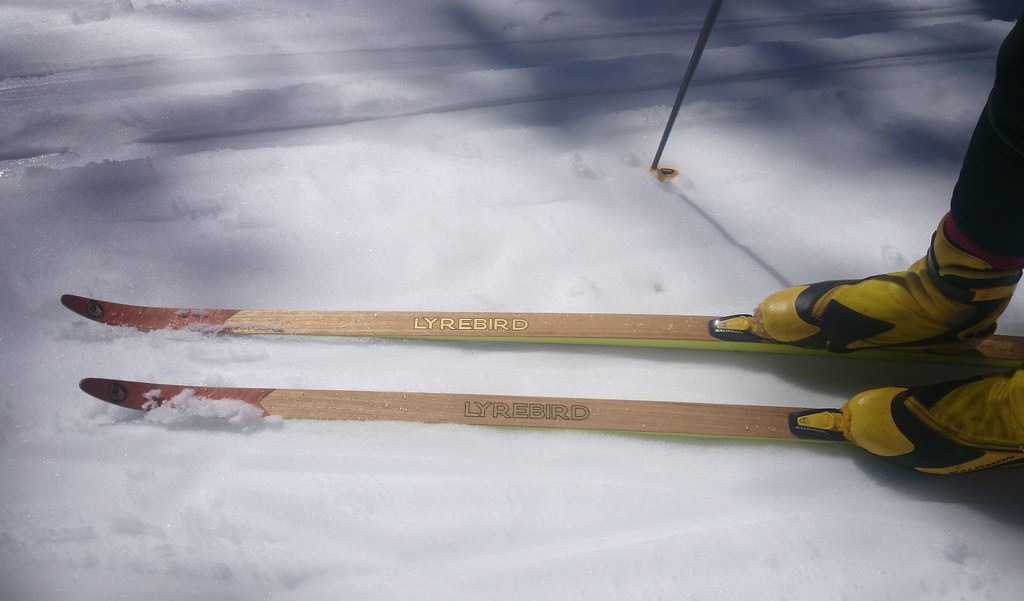
DSC_0246
Katherine takes pretty good pics using just a phone.
Mark Kelly
-
-
Re: Jig development again
Mark - I haven't looked into it yet to check, but... I'm pretty sure I saw a Lyrebird on my ride this morning, in the Ku-Ring-Gai National Park (just north of Sydney). Is that possible / likely?
And yes, I was on my Lyrebird!
-
Re: Jig development again
Not one of mine.
There is precisely one person in Sydney with one, and he has two. Hog.
Mark Kelly
-
Re: Jig development again
Erm, I meant the bird...!
-
Re: Jig development again
Ahh, sorry.
Dunno about Ku-Ring-Gai but I know there's a population in RNP at Audley, so it's at least possible.
Mark Kelly
-
Re: Jig development again
Hmmm, not convinced now - it sort of looked like the pic below (which is a Lyrebird) from memory, but it legged it when I tried to go back for a pic. I recall two distinct tail feathers, but they were more like the whispy ones than the dense, dark ones.
-
Re: Jig development again
Mark Kelly
-
Lyrebird numbers on the rise.
Mark Kelly
-
Small coincidences
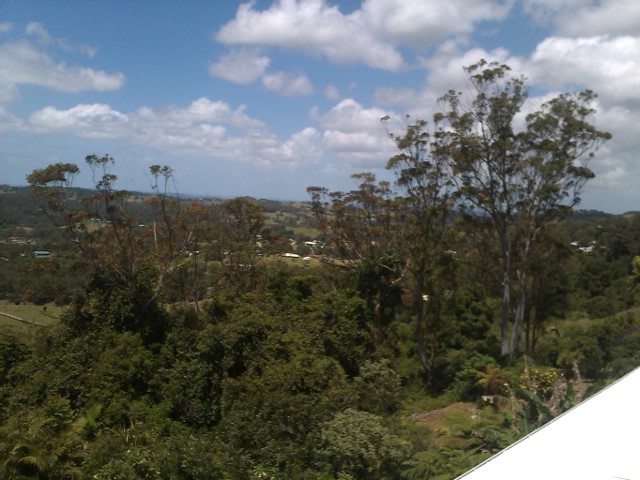
Mums
Currently away looking after the Aged P.
The above pic is from her back verandah, the trees in the foreground are Eucalyptus grandis, my go -to wood for lateral stiffening on the bikes.
Mark Kelly
-
Re: Small coincidences
Finally got the tester running.
Mark Kelly
-
ISO4210_6 tester
Slightly better (but still crap) video of tester running.
Mark Kelly
Similar Threads
-
By Boedie in forum Smoked Out
Replies: 30
Last Post: 11-22-2014, 05:45 PM
-
By magnoliacycles in forum Smoked Out
Replies: 25
Last Post: 04-11-2011, 04:57 PM
Posting Permissions
- You may not post new threads
- You may not post replies
- You may not post attachments
- You may not edit your posts
-
Forum Rules
Bookmarks